A True Digital Master Schedule, made by our employees for our employees
by Sebastien Wickert
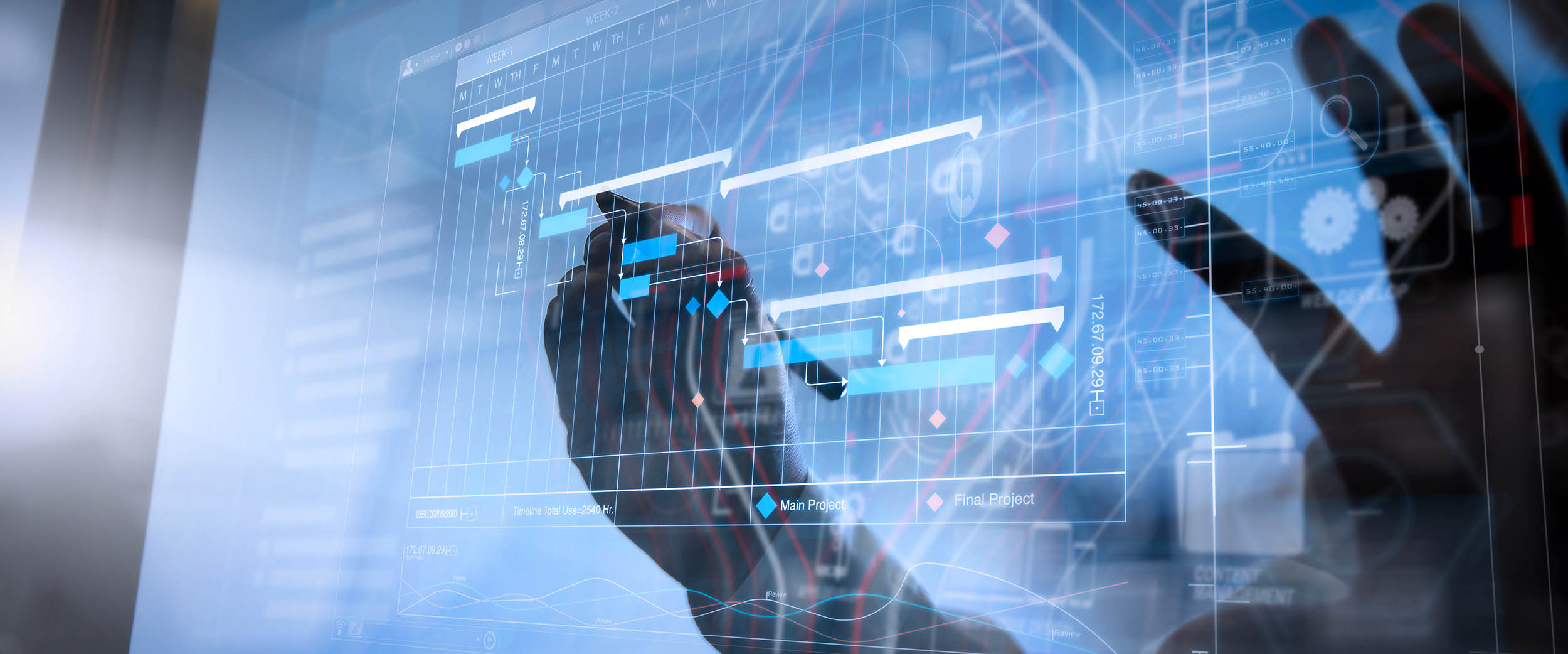
It could be aggregate, HMA, grading or any other type of work, all our daily operations revolve around scheduling. We line up raw materials, vehicles, assets and crews to execute a job. And for the job to be a success we need perfect communication between our divisions and employees with a schedule that is always up to date.
In the past, every division had their own calendar and schedule. Sometimes it was a whiteboard, a paper form or an Excel spreadsheet. Their common drawback was the lack of collaborative capabilities and real time updates.
Early last year, our Manufacturing Engineer and our Construction Manager, from our company Sully-Miller in California, recognized the necessity for combining the forecasting and scheduling demands of multiple asphalt manufacturing plants, raw aggregate production, construction and trucking needs into a collaborative common platform.
Together, we decided to create a system that would centralize and capture accurate, real-time information of our operations that would accessible by everyone on multiple devices using the free Microsoft tools at our disposal. After one month, we had a working prototype that the team at Sully-Miller was able to use. Within a month and supported by Sully-Miller’s President Bill Boyd, it was decided to switch the construction and manufacturing division onto this Master Schedule.
Before the summer, other regions had heard about it and asked to try it. Branscome, Barrett NYN and Delta all started to use the Master Schedule. They knew that it was only the first version and many things needed to be improved. Regardless, they saw the potential and kept giving feedback and ideas for new features.
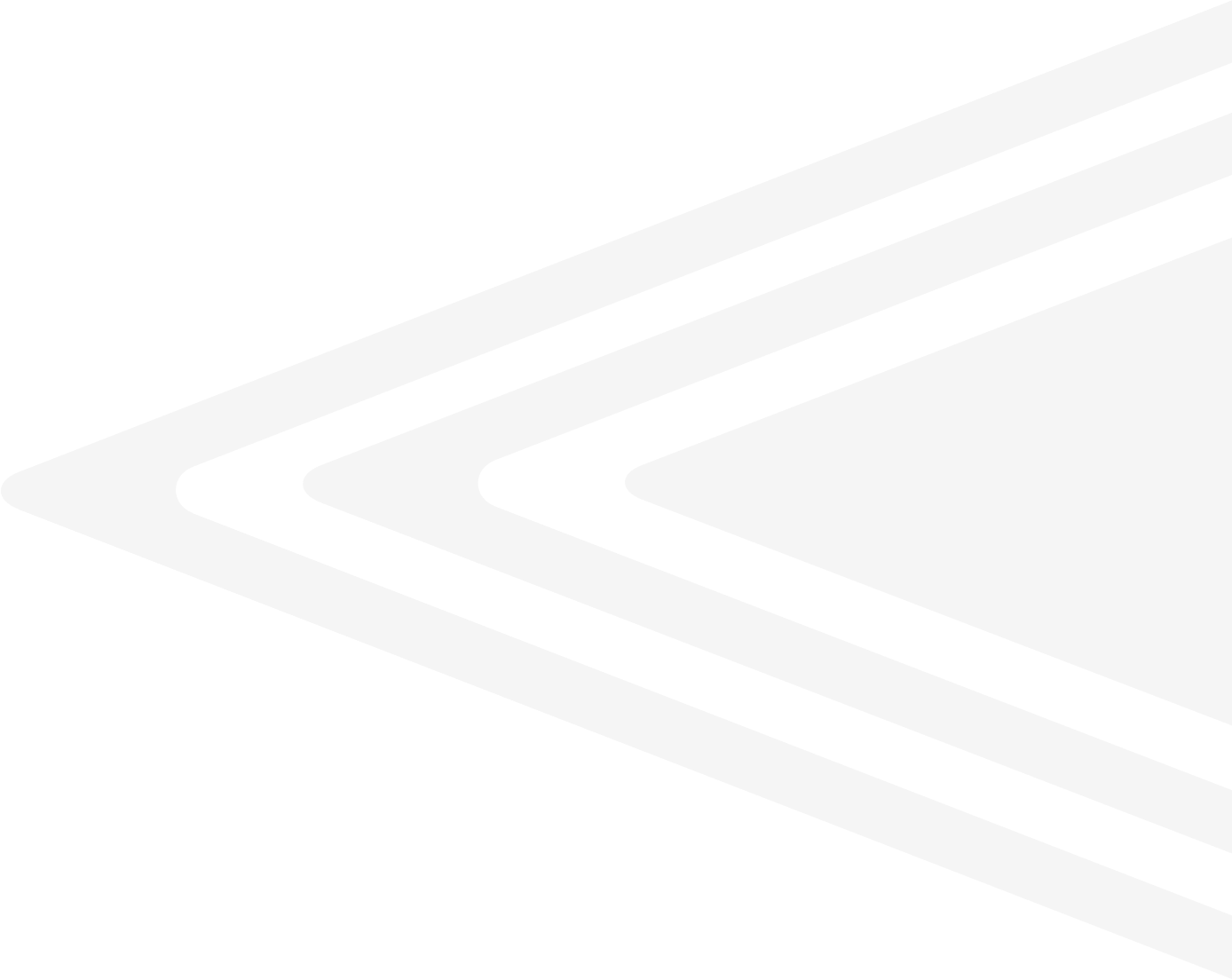
By the end of the season 2019, we had time on our side to build the version 2. Our team did an amazing job taking all the feedback and great ideas we received while simultaneously making the user experience more efficient and user-friendly. We released the new beta version in February with a few companies and kept using their feedback to improve it. Now, everyone from estimators, to management, including plant operators and foremen in the field with their iPad can access an always up-to-date schedule and get all the information on their projects.
Four major upgrades in version 2 are
- the connection to JDE to avoid retyping info we already had in JDE,
- a simpler way to move shifts around as well as set blackout dates on the projects,
- alerts when a shifts is canceled or modified,
- the addition of a multi-activities schedule.
The latter essentially means that we can now track the manufacturing and paving schedules, the milling schedule, the external aggregates sales, trucking needs, etc. all in one place.
With all these new features, The Master Schedule is now a true scheduling tool and can work for all our companies in the US. One thing we are certain of is that the next version will be even better thanks to the feedback from our users.